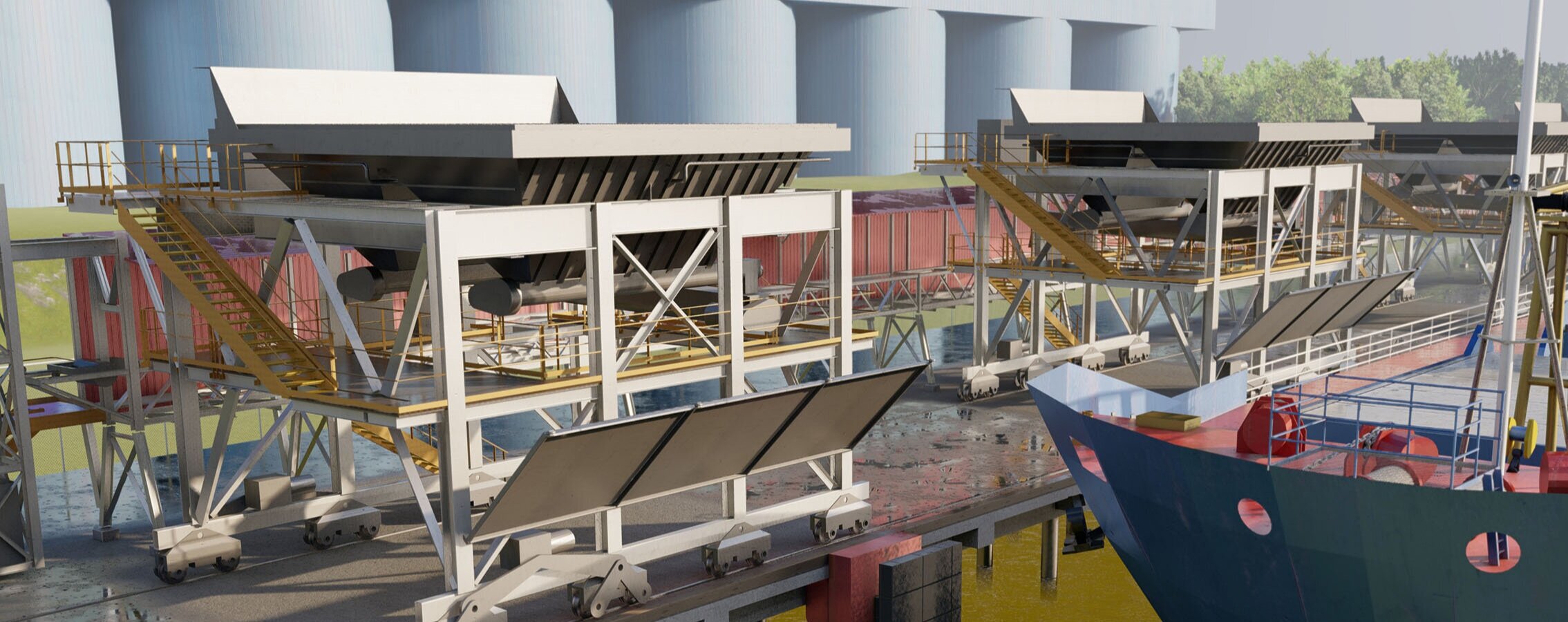
MOBILE HOPPER UNLOADING SYSTEM
AMI was contracted to provide engineering services for the design of upgrading the unloading process along an existing wharf. The new system included four new mobiles hoppers that accommodate self-unloading vessels, two new belt conveyors, and two new bucket elevators. Challenges of this project included limited installation windows and sequencing requirements to allow dock operations to continue with minimal impact to production capacity. AMI worked closely with the client from feasibility to construction oversight to provide a highly customizable solution with comprehensive construction phasing.
AMI utilized 3D concepts at early stages that allowed the client to visualize key concepts and explore alternates at a low cost. AMI developed an AACE Level 3 cost estimate of the preferred solution at 30% design for budgetary planning and bid control within 4 weeks of receiving the PO. AMI offered an expedited path to hard bids in the form of sleek bid packages with fabrication level models and less drawings. AMI also assisting with bidder qualifications & bid comparisons. AMI partnered with our client’s preferred vendors and delegated design to these experts to ensure a high-quality product with warranty.
Throughout the bidding and construction process AMI remained present to assist the client with bidder qualifications, managing the RFI tracking system, providing prompt responses to RFI’s, developing and overseeing QA/QC procedures, and engaging in regular progress meetings with the contractor throughout the construction process. Utilizing a unique workflow and the latest technology, AMI was able to focus attention on QA/QC.